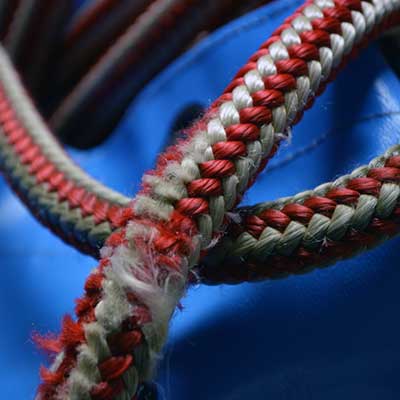
Rope Safety, Working Loads and Breaking Strains
We’ve spoken on these pages before about the importance of good rope care, such as keeping your rope clean, using a rope bag and properly coiling your rope. All these good practices will help ensure your rope has a healthy long life but as important as this is, it’s also essential to understand when your rope needs to be replaced.
However much you’d rather not shell out another hundred quid or so on another rope, it really is a small price to pay to make sure you and your staff are safe when working at height.
In this article we’ll take a look at rope safety, and when to replace your rope. We’ll then go on to give a breakdown of stats on the climbing ropes we supply at Landmark Trading as part of our arborist’s equipment range.
Rope Inspection and Age
The first is to inspect your rope before you use it. It’s inevitable that ropes will, over time, become frayed and damaged by constant friction and heat. Quite often, damage can happen without you noticing, so even if you’re sure the rope is in good nick, it really does pay to take the time to inspect it properly.
To inspect your rope, run the whole length of it through your hands. As well as obvious fraying or damage to the sheath, you’re looking for flat spots, which indicate that the fibres have become deformed – due it having to absorb fall impacts. Other signs that you should replace the rope will be melting, stiffness, and nicks in the sheath that expose the core.
In terms of general wear and tear, there really isn’t a hard and fast rule as to exactly when you should replace a rope; it depends on how often it is used, the extent of wear, level of exposure to UV and many other factors. Whilst ‘fluffing’ on the surface of the rope is normal wear and tear, if you find broken or damaged strands, melted patches, flat spots, or the core is at any point exposed you should replace it. If in any doubt, get advice from your LOLER inspector. Bear in mind that even ropes that aren’t being used will degenerate over time and a rope should never be used beyond the maximum service life guidance given by the manufacturer.
Falls
Arborists aren’t likely to take a fall on a rope as they should always be correctly anchored to prevent – or at least minimise – this. If your rope does sustain a fall, it should be retired immediately as this could have significantly compromised the strength of the rope.
Compliance
Tree surgeons and arborists legally have to subject all climbing equipment to independent inspection every six months (this includes ropes). All this equipment must comply with “Lifting Operations and Lifting Equipment Regulations” (LOLER) as set out by the Health and Safety Executive. Lowering and rigging equipment must be inspected every 12 months.
This must be undertaken by a ‘competent person’ and there is potential for a conflict of interests here if that person has a vested interest in not decommissioning expensive tree surgery equipment (ie they work for the company that purchased it). This article from Eco Tree Care has a lot more info on the subject. You can also check out the HSE LOLER Guidelines.
Climbing Rope Working Loads and Breaking Strains
Let’s take a look at the breaking strains of the various ropes available from Landmark Trading. Note that these are all tree climbing ropes and are designed to support people. These shouldn’t be confused with lowering ropes, which are static and have less elasticity. These are designed to lower branches and not people.
Before we begin, let’s demystify some of the common terminology you may encounter when shopping for a rope. Because climbing ropes usually have way in excess of the strength required for a person’s weight, the terms MBS and SWL are a lot less relevant to climbing ropes than they are to lowering ropes, but its good to have an understanding of the terms:
- MBS (minimum breaking strain): This represents the force required to make the rope fail or yield, so in other words, if you put this force on the rope you’d expect it to break.
- SWL (safe working limit): this is the force that can be applied to a rope (or any other piece of lifting equipment) to lift, suspend or lower an object without fear of breaking, and includes a margin of safety. It is sometimes referred to as working load limit (WLL).
The Safe Working Limit of a rope is calculated by dividing the Minimum Breaking Strain by a safety factor. For example, a rope with a 2500kg MBS, using a factor of 10 if in use for PPE, would give a Safe Working Load of 250kg. This means that your rope can be expected to safely take a 250kg load and in addition has a substantial safety margin before reaching a potential breaking point.
You should be aware that tying a knot in a rope significantly reduces the strength of the rope. If using a knot, you should deduct 30-40% off the MBS before applying the safety factor to calculate your SWL.
All the climbing ropes we stock at Landmark Trading conform to the EN1891 international rope safety standard.
New England Tachyon
- Diameter: 11.5mm
- Available Lengths: 35m, 45m, per metre
- Breaking Strain: 2570 kg
New England HiVee
- Diameter: 13mm
- Available Lengths: 37m, 45m
- Breaking Strain: 2650kg
Marlow FCR Climbing Rope
- Diameter: 13mm
- Available Lengths: 15m, 35m, 45m, per metre
- Breaking Strain: 2750kg
Marlow Aeris
- Diameter: 11mm
- Available Lengths: 8m, 15m, 35m, 45m
- Breaking Strain: 3140kg
Marlow Gecko
- Diameter: 13mm
- Available Lengths: 35m, 45m
- Breaking Strain: 3263kg
Yale XTC Plus & Fire
- Diameter: 13mm
- Available Lengths: 37m, 45m, per metre
- Breaking Strain: 2812kg
Edelrid X-Perience 13mm
- Diameter: 13mm
- Available Lengths: 35m, 45m
- Breaking Strain: 3000kg